Lexus of North Miami started as solely a dealership. That changed in 2009, when it followed in the footsteps of Lexus of Pembroke Pines, which had added a collision center 20 years prior in 1999.
“We converted half of the service department at Lexus of North Miami into a body shop with outside paint booths,” said Brian Martin, director of auto collision at Lexus of North Miami Collision Center and Lexus of Pembroke Pines Collision Center. “Then Lexus of Pembroke Pines Collision Center won Lexus Collision Shop of the Year in 2012, and Lexus of North Miami Collision Center won Lexus Collision Shop of the Year in 2018.”
Lexus of North Miami & Lexus of Pembroke Pines
North Miami & Pembroke Pines, FL
786-528-3926 & 954-443-2770
www.craigzinncollisioncenters.com
Company At A Glance...
Type: Collision Repair
Facility Employees: 110
In Business Since: 2009 (North Miami), 1999 (Pembroke Pines)
Number of Locations: Two
Combined Production Space: 90,000 square feet
Martin, who has held his position for 17 years, said he feels the shops earned these accolades by “focusing on fixing the car right from the beginning.”
“We work for the customers---there’s no greater focus we have than providing excellent customer service,” he said. “And in light of all the challenges we face from the insurance industry to using aftermarket and salvage parts, paint reduction and more, we stay steadfast on working for the customer, in hopes that they buy their second vehicle from us regardless of where they bought their first one.”
On top of a Lexus certification, both locations have collision repair partnerships with Nissan, Infiniti, Honda, Acura, Hyundai, Kia and Fiat, as well as I-CAR Gold Class titles.
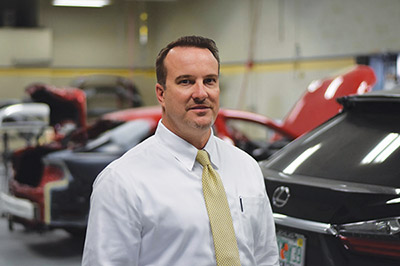
Martin said since Lexus of North Miami Collision Center and Lexus of Pembroke Pines Collision Center use OEM parts, they implement equipment and products that meet factory standards. So, when it came time to find a company to provide diagnostic data for the scanning and calibration processes, the same rule applied.
“In the last few years, calibrations have been a huge point in the repair process and returning cars to their pre-loss condition,” Martin said. “And since we are part of the Collision Advice Legacy Group with Mike Anderson, we had been attending those meetings, and it was very evident how important calibrations were for a quality repair.”
Martin explained with the sheer volume of cars at each location---more than 300 repair orders a month---“it became a challenge for the facilities to promptly complete all calibrations and pre- and post-scans.
“An essential part of why we chose asTech is because their certified technicians run OEM equipment for all calibrations and pre- and post-scans,” he explained. “These calibrations are not being done with any aftermarket equipment.”
Lexus of North Miami Collision Center and Lexus of Pembroke Pines Collision Center house John Bean machines from asTech. Martin said the asTech devices hook up to cars in each shop so in-house technicians can communicate with asTech technicians in Texas.
“One of the main benefits of using asTech is having the pre- and post-scans printed,” he said. “This allows us to understand the vehicle damages when they arrive at our facility and also helps us determine what is related and not related to the accident.”
Martin explained why having this printout gives them peace of mind.
“We receive a printout and a copy that state how all the calibrations were completed,” he said. “That way, if we have a return and somebody tries to say, ‘Well, you guys didn’t fix something correctly,’ we have a date and timestamped report showing exactly when and what we did.”
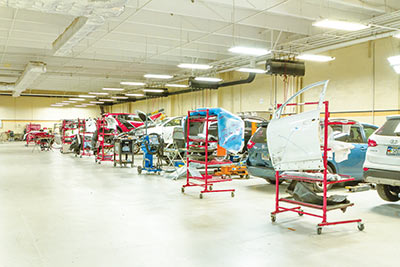
Martin said the printouts are also very important to their insurance partners.
“Our insurance partners prefer to have those reports when the cars come in because it helps them also determine if the damage at hand is related to the loss,” he explained. “This is possible because the asTech reports give specific information to the code that may be on in the car.”
Martin said the average vehicle at Lexus of North Miami Collision Center and Lexus of Pembroke Pines Collision Center has between two and four calibrations, not including the pre- and post-scans.
“Using asTech for calibrations has allowed our facility to decrease cycle time by approximately two days while increasing the quality of the repair,” he said. “Plus, the asTech portal makes it possible for our associates to access all invoices and scan reports minutes after the scans finish.”
Martin said Lexus of North Miami Collision Center and Lexus of Pembroke Pines Collision Center consider asTech one of their essential business partners.
“At the end of the day, if a shop isn’t performing calibrations, they’re not returning the car to pre-loss condition,” he said. “If you’re not calibrating the blind spot monitor, how do you know where the radar is aimed? If there is a lane keep assist in the front, how do you know without calibrating that the lane keep radar is aimed toward the center of the road? So, when you’re not returning a car to pre-loss condition, it creates a lot of liability."
asTech, Driven by Repairify
888-486-1166
astech.com
Facebook: @astechdrivenbyrepairify
Instagram: @asTech_official
LinkedIn: @astechdrivenbyrepairify
To read more auto body shop profiles from the June 2023 Shop and Product Showcase, click here.